Testing of metal products
We carry out testing of chemical composition, structure and mechanical properties of mainly metal products. This ranges from simple measurements, through complex studies to multi-faceted research expertise.
We are happy to support industrial plants in solving technological problems, determining the causes of material defects, corrosion and component damage. We operate in a broad spectrum of topics and are not afraid of challenges.
Our laboratory meets the requirements of PN-EN ISO/IEC 17025:2018-02 and has been accredited continuously since 1997.
ACCREDITED TESTING
Testing of chemical composition by spetrometric method:
Microstructure observations using an optical microscope:
In the laboratory, we have the necessary equipment for metallographic preparation. We can observe samples using an optical microscope equipped with image analysis software, including steel products, cast iron and non-ferrous metals and their alloys.
We perform the microstructure examination according to standards:
- PN-H-04504:1963 (Microstructure testing of steel metallurgical products – Tertiary cementite – Banding – Widmannstaetten structure);
- PN-H-04505:1963 (Microstructure of steel metallurgical products – Standards and determination);
- PN-H-04517:1992 (High speed steel – Bars – Test methods for carbide segregation);
- PN-H-04661:1975 (Ductile and malleable grey cast iron – Metallographic tests – Determination of microstructure);
- PN-EN ISO 945-1:2019-09 (Microstructure of cast iron – Part 1: Classification of graphite separations by visual analysis);
- PN-EN ISO 1463:2021-10 (Metal and oxide coatings – Measurement of coating thickness – Microscopic method);
PN-EN ISO 3887:2018-03 (Steels – Determination of the depth of decarburisation).
We carry out the following tests:
- microstructure analysis,
- quantitative and qualitative analysis of structure components,
- measurement of thickness of metallic and oxide coatings / layers,
- evaluation of depth of decarburisation,
- evaluation of carbide segregation,
- evaluation of graphite separations in cast iron,
- assessment of metallurgical products.
Observations of surface structure and topography by scanning electron microscopy:
Determination fo mechanical properties:
Determination of forces and displacements in static tension, compression or bending tests up to 1 000 kN and fatigue tests up to 100 kN.
We have 3 strength testing machines with different force ranges (20, 150, 300; 1,000 kN).
We carry out tests in accordance with standards:
- PN-EN ISO 6892-1:2020-05 method B (Metals – Tensile test – Part 1: Test method at room temperature);
- PN-EN ISO 7438:2021-04 (Metals – Bending test);
- PN-EN ISO 8491:2005 (Metals – Pipes – Bending test);
- PN-H-04320:1957 (Static compression test of metals).
Hardness measurements by Brinell, Vickers, Rockwell, Knoop method:
In the laboratory we carry out the followong tests:
- Brinell hardness HBW – indenter: ball with diameter of 2.5 mm and 5 mm according to PN-EN ISO 6506-1:2014-12 (Metals – Measurement of hardness using the Brinell method – Part 1: Test method);
- Vickers hardness HV – scale range HV 0.05, HV 0.1 HV 0.3, HV 0.5, HV 2, HV 10 according to PN-EN ISO 6507-1:2018-05 (Metals – Measurement of hardness with the Vickers method – Part 1: Test method);
- Rockwell hardness – HRA, HRC range – according to PN-EN ISO 6508-1:2016-10 (Metals – Measurement of hardness using the Rockwell method – Part 1: Test method);
- Knoop hardness HK – range HK 0.1 according to PN-EN ISO 4545-1:2018-04 (Metals – Measurement of hardness by the Knoop method – Part 1: Test method).
Charpy impact test:
The test is carried out in accordance with EN ISO 148-1:2017-02 Metals – Charpy impact test – Part 1: Test method, at temperature reduced to -196°C (liquid nitrogen) and room temperature.
Impact testing is carried out, among other things, to compare materials, determine the temperature of transition to brittle state or assess the compatibility of tool steels for hot work.
Thanks to the experience we have gained, we are able to provide our customers with an additional service – material expertise in the field of metallurgical defects in materials, i.e. non-metallic inclusions, material discontinuities, fatigue cracks after forging, testing of metal sheets for delamination (lamellar cracks), anisotropy of metal sheets, determination of the class of bolts and nuts, and determination of operating defects aimed primarily at determining the cause of crack formation.
We examine, among other things: fasteners, forgings, spindles, hooks, railway and tramway rails, traction elements, vehicle wheels, causes of corrosion, causes of cracks in welds and structures, determine the temperature of transition of a material into a brittle state, etc.
We also offer determination of conformity with the manufacturer’s declaration in accordance with the subject standards.
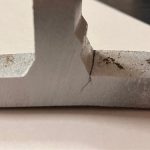
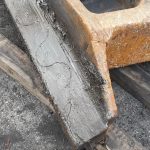
Our research reports are recognised in all signatory countries of the ILAC MRA Multilateral Mutual Recognition Agreement.
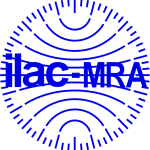
Our specialist:
Mateusz Kukliński
Łukasiewicz Research Network – Poznań Institute of Technology, Materials Testing Laboratory, Jana Pawła II St. 14, 61-139 Poznań.
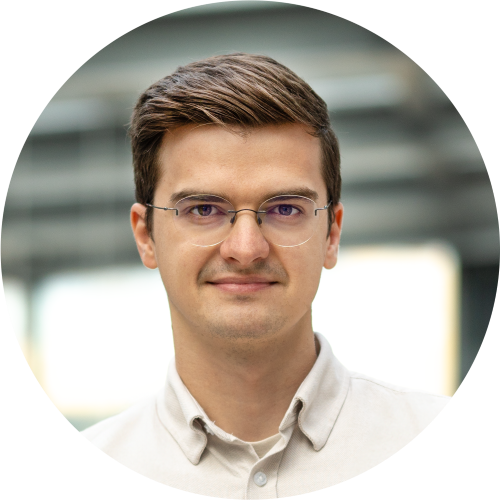